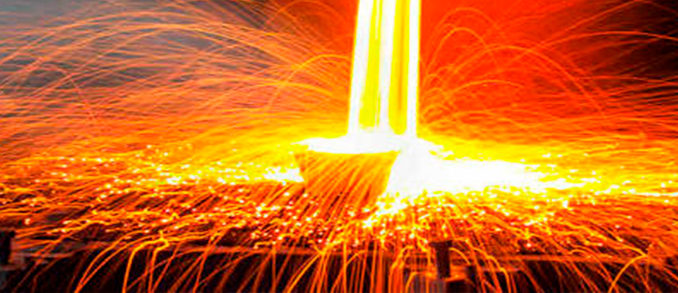
Reforma das máquinas de sínter trouxe estabilidade para empresa
As exigências por estabilidade e disponibilidade dos equipamentos, otimização dos processos, elevação da produtividade e qualidade objetivando a produção a custos competitivos são continuamente crescentes.
Dentre deste contexto, a finalidade deste artigo é apresentar o Upgrade da Sinterização de uma grande siderúrgica brasileira realizada com a reforma de máquinas obsoletas levando a maior confiabilidade e a estabilidade operacional da Planta de Sinterização.
O processo de sinterização de minério de ferro é empregada no setor metalúrgico para transformar finos de minério, através da aglomeração junto com outras matérias primas, em um produto denominado sínter.O sínter é uma fonte metálica para carregamento dos alto-fornos e que possui características físico-químicas definidas e apropriadas para operação. O processo se inicia na queima superficial da camada de mistura, processo chamado de ignição, provocado pela liberação de calor proveniente da queima de gás no interior do forno de ignição.
Sabe-se que, fatores tais como integridade dos equipamentos, estabilidade operacional e aspectos relacionados às matérias primas são fatores de suma importância para o processo de sinterização.
A unidade da Sinterização segue, dentro desta filosofia, em a busca constante da excelência na realização de suas atividades, por conseqüência no seu produto, o sinter. A Sinterização está alinhada a este objetivo, visto que o sinter é o principal elemento constituinte da carga metálica dos Altos-fornos, com participação próxima a 70%. Por isso, a estabilidade da planta é fator chave para uma boa performance dos Altos-fornos.
Alguns fornos operam com gás de coqueria ou gás natural, a depender do tipo de forno. O forno de projeto atualmente opera com 100% de gás proveniente da coqueria (Coke Oven Gas – COG).
A queima superficial se torna muito importante, pois sua eficiência contribui para menor geração de “soft sinter”, que é um material de qualidade inferior formado superficialmente no leito a sinterizar.
No decorrer dos anos, o gás de coqueria produzido nessa siderúrgica vem apresentando uma redução significativa em seu PCI (poder calorífico inferior – Kcal/m3 ) e com isso ocasionando deficiência na ignição do forno da sinterização.
Com o empobrecimento da queima, houve uma queda na temperatura de trabalho do forno de ignição chegando a uma temperatura média de 1085ºC, bem abaixo de sua temperatura de projeto (1200 ºC).
Além da condição do gás mencionada anteriormente, o controle de combustão era realizado de forma manual através da ação direta dos operadores na regulagem da vazão de ar, provocando perturbações no processo e consequentemente efeitos colaterais negativos na qualidade do sínter e produtividade final da planta.
O objetivo desse projeto foi remodelar a filosofia de operação do forno ignição e a reestruturação das malhas de controle existentes e a implementação da metodologia de controle com limites cruzados, de forma a conseguir aperfeiçoar a queima através de ganho de poder calorífico mesmo com a condição de PCI reduzido do gás de coqueria.
Através das reformas realizadas e melhorias implementadas obteve-se maior confiabilidade dos equipamentos, com melhor estabilidade operacional da planta de Sinterização.
Ressalta-se que, após a reforma do Resfriador, uma atuação inédita na siderúrgica desse projeto, foi possível verificar a redução da temperatura de descarga do sinter do Resfriador para as correias da linha de sinter produto, para abaixo de 100°C. Isto foi possível, pois houve além do aumento da área útil do equipamento de 400 para 516,6 m2 , também a elevação do volume de sopro de ar dos ventiladores de 39.000 para 46.800 m³/min.