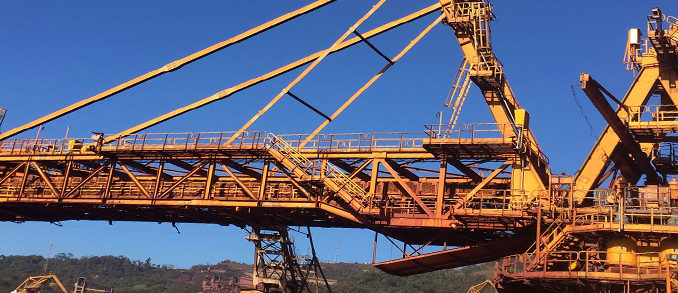
The escalating demand for industrial automation has compelled machine manufacturers to reconsider their design processes. In this article, we will delve into the significance of manufacturers embracing a design tailored for autonomous machines from the outset and delve into the adverse impacts that subsequent adaptations can exert on the performance of these machines.
When crafting machines for autonomous operation, manufacturers must weigh various factors, including advanced system integration, connectivity, safety, and usability. An adept design involves incorporating specific features that streamline the transition to automation, negating the need for significant modifications down the line.
This entails fabricating machines that seamlessly integrate into autonomous systems and advanced technologies, allowing for future updates and adjustments without imposing major modifications on the facility.
By adopting an adaptable design approach, manufacturers can proactively anticipate automation needs and incorporate features conducive to the integration of autonomous systems. This encompasses installing standardized communication interfaces, establishing mounting points for sensors and actuators, and implementing modular structures facilitating the inclusion of additional components.
A prevailing trend in industrial automation is the reduction, or even elimination, of operator cabins in yard machines. With technological advancements, remote control systems, augmented reality, and artificial intelligence empower machines to be operated and monitored from a distance, obviating the need for the physical presence of operators within cabins.
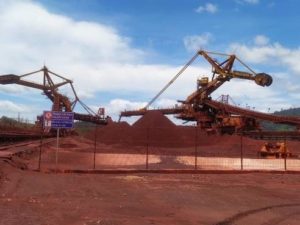
The absence of cabins yields various benefits, such as:
- Reduction in manufacturing costs.
- Augmented operational flexibility.
- Heightened safety for operators.
- Simplification of maintenance procedures.
- Optimization of space in the industrial yard.
Moreover, remote operation enables operators to monitor and control multiple machines simultaneously, thereby enhancing operational efficiency.
The removal of the local operator cabin and all devices necessary for local manual operation results in savings ranging between 3% and 5%, typically adequate to offset the investment in autonomous technology for that machine.
Manufacturers should institute robust safety systems, including presence detection sensors, emergency stop systems, and safety protocols, to ensure the integrity of operators during remote operation.
The absence of a tailored design culminates in subsequent adaptations that can compromise operational efficiency and detrimentally impact machine performance.
Subsequent adaptations to retrofit an existing machine into an autonomous one can be intricate and time-consuming. Integrating autonomous systems necessitates modifications to machine components, communication interfaces, and control systems. These adaptations may precipitate compatibility issues, communication conflicts, and technical challenges, adversely affecting the overall machine performance.
Subsequent adaptations entail additional costs, such as hiring automation experts, acquiring new components, and downtime to effectuate the necessary modifications. Additionally, machines remain inactive during the adaptation period, precipitating production interruptions and financial losses.
Manufacturers should recognize the paramount importance of a design pre-adapted for autonomous machines, with the aim of optimizing operational efficiency, productivity, and safety.
The absence of a pre-adapted design begets intricate subsequent adaptations, incompatibilities, risks of failures, and augmented costs and downtime.
Leia mais artigos como esse aqui.