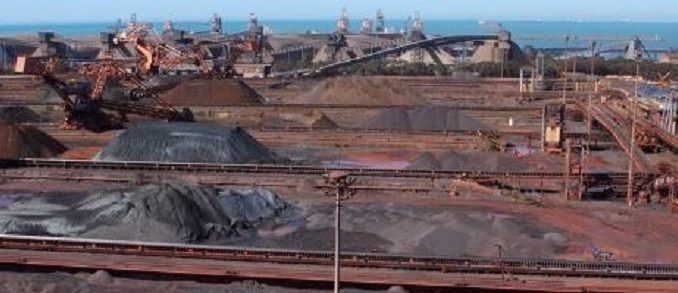
Automação do Processo de Recuperação
O processo estocagem de minério em pátios é essencial para a logística de carregamento de vagões ferroviários e navios, permitindo o escoamento do minério para seus diversos destinos. Na indústria este processo vem passando por aprimoramentos tendo como seu auge operacional a automatização das máquinas e processos, com a implementação de novas funcionalidades utilizando recursos realtime de mapeamento 3D dos pátios, controle de posição dos equipamentos com precisão de centímetros e comunicação multiponto. Essa iniciativa visa reduzir a variabilidade na taxa de recuperação e aumentando a eficiência e produtividade dos terminais.
Pátios de estocagem, Funcionamento:
Os terminais de escoamento de minério possuem uma estrutura robusta e tecnologicamente atualizada. O Centro de Controle Operacional (CCO) monitora em tempo real as operações de programação de navios, descarga, empilhamento e recuperação do minério no pátio.
É comum que em grandes terminais alimentados por ferrovia a área de descarga conte com a presença dos viradores de vagões, que recebem o minério transportado pela estrada de ferro e dali são redirecionados por transportadores até o pátio de estocagem. O terminal Ponta da Madeira no maranhão conta com 8 viradores que atendem o escoamento da Estrada de Ferro Carajás.
Os pátios são compostos por áreas variando a quantidade de acordo com a demanda do terminal, no brasil temos pátios com 13 áreas de estocagem que armazenam até 9 milhões de toneladas de minério. A movimentação de material nos pátios é feita por empilhadeiras e recuperadoras de minério. Os terminais marítimos operam com a logística de píeres e berços de atracação, que permite realizar um carregamento mais eficiente dos navios.
Automação do Processo de Recuperação e Empilhamento:
A exemplo do Terminal Marítimo Ponta da Madeira (TMPM), a recuperação do minério atualmente é realizada de forma remota, por operadores alocados em uma sala de controle central amparado por sofisticados sistemas de supervisão e teleoperação. A automatização desse processo visa limitar a intervenção humana no intuito de reduzir a variabilidade da taxa de recuperação assim aumentando a eficiência e previsibilidade operacional não só dos pátios mais do terminal como um todo, uma vez que os sistemas de gestão de ordens e operação passam a trabalhar de forma integrada.
Na recuperação em modo automático, o operador apenas informa os dados quantitativos e qualitativos do carregamento, solicita o planejamento de bancada, avalia o plano criado pelo sistema e autoriza a execução.
O sistema calcula e apresenta a melhor logística de recuperação levando em consideração informações como as características e disposição do material no pátio e o mapa de restrições das máquinas e rotas até o navio, após o aceite do operador, que com a automatização dos pátios passa a assumir o papel de supervisor do processo, o sistema assume o controle de todos os movimentos das recuperadoras desde o posicionamento inicial até a troca de bancadas.
As máquinas realizam os movimentos necessários, respeitando o plano de bancadas utilizando informações do mapeamento 3D feitas em tempo real das pilhas de minério.
Benefícios da Automação no TMPM:
A automatização do processo de recuperação e empilhamento de minério trouxe diversos benefícios para o Terminal Marítimo Ponta da Madeira sendo o principal deles, os ganhos de produtividade alcançados por meio da estabilização da taxa de recuperação, ganhos estes que somados aos ganhos na segurança operacional obtidos com a teleoperação das máquinas de pátio elevaram o status de maturidade operacional do terminal a um nível sem precedentes no cenário mundial.
Estudos realizados pelas empresas do mercado indicam que a automação principalmente do processo de recuperação com sistemas que utilizam tecnologias de mapeamento 3D em tempo real vem se consolidando como os mais eficientes na e diminuição da taxa de variabilidade durante a recuperação do minério no pátio.
Além disso, podemos citar outros benefícios como:
- Redução dos custos operacionais, por meio da otimização da utilização de recursos humanos e dos ativos de produção.
- Redução dos custos de manutenção, obtida ao melhorar a operação dos equipamentos em modo automático o que aumenta a disponibilidade física desses ativos.
- Redução das perdas de produção, com a utilização do recurso de mapeamento 3D na logística de escoamento do minério.
- Redução do consumo de energia, graças ao aumento do desempenho operacional.
Leia mais artigos aqui.